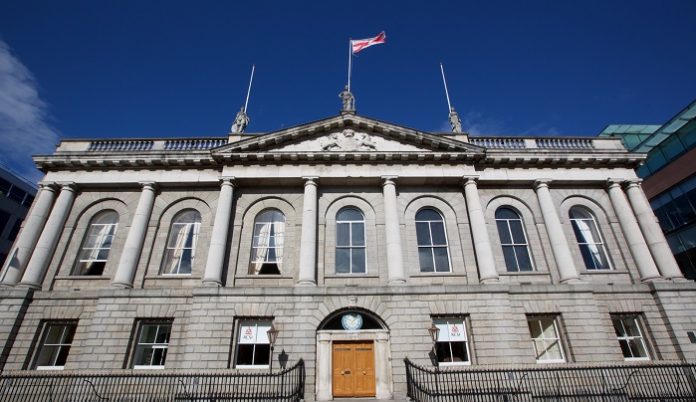
An institution’s size does not have to limit its ambition, as the Royal College of Surgeons in Ireland is proving. The college, ranked in the top 250 of the Times Higher Education (THE) world rankings, is using lean to help it achieve its goals in a complicated environment, as Doreen Gilfedder explains.
A key characteristic of Lean philosophy is its high level of applicability. One of the lessons we have learned at the Royal College of Surgeons in Ireland (RCSI) is that a smaller institution is not necessarily at a disadvantage when it comes to applying lean. While larger institutions may have more resources at their disposal, lean thinking is often more readily achievable in a smaller institution.
Additionally, smaller institutions are often more flexible and responsive to change. The benefits of this agility to respond to changing circumstances should not be underestimated; the veritable changing of course of a boat, rather than an iceberg.
As the primary academic partner of the RCSI Hospitals Group, one of Ireland’s seven networks of hospitals, the college is tasked with stimulating a culture of learning and openness to change within its geographically-dispersed member institutions.
RCSI is also international, with operations in Bahrain, Dubai and Malaysia, and has a global profile with its position as joint first out of the eight institutions in the Republic of Ireland included in the THE world university rankings.
Yet the college is a relatively smaller higher education institution that operates a self-funding model. This represents a complicated, multi-disciplinary environment in which to achieve its strategic objectives.
This is where lean comes in. It provides a quality and improvement method to engage multiple stakeholders and achieve strategic objectives. To do this we established a Quality and Process Improvement Centre during 2016 to support a multi-faceted culture of continuous improvement.
The centre, which is led by executive director Kieran Tangney, has the following goals:
- To integrate quality and improvement approaches within the RCSI education curriculum, both at undergraduate and professional level;
- To creatively engage RCSI’s clinical partners with a view to implementing practical process improvement to make a difference at patient level;
- To provide a disciplined approach to the application of continuous improvement at strategic and operational level internally within RCSI to support the growth strategy and to positively impact on staff, students and all stakeholders.
The lean journey at RCSI is just beginning. However, key learnings have emerged from both the initial pilot projects and the early work performed by the Quality and Process Improvement Centre:
Top Tips
- Respect for people is paramount. In a smaller institution, it is vital to engage organisational support systems.
- Ensure both the sponsorship and commitment of senior management and leadership.
- Create competency internally through education and dissemination of quality knowledge of Lean.
- While lean should be the preserve of all, the creation of lean champions can help reach a tipping point, typically easier to achieve in a smaller institution.
- Build multi-functional teams, leveraging existing internal expertise, in particular IT and HR skillsets.
- Empower front-line staff to make change and embed Lean thinking.
- Engage partners from across your value chain.
- Generate an emotional attachment to Lean by focusing on people and positioning Lean as an improvement philosophy rather than a remedial one.
- Concentrate on your CSFs, your critical success factors. Make friends with the Pareto rule which states that, in many cases, roughly 80% of the effects come from 20% of the causes. Segregating the vital few from the trivial many ensures optimal allocation of the scarce resources in a smaller institution. In our experience, the Pareto rule has held true; focusing on the top 20% of issues identified can deliver 80% of the required solution.
In a similar vein, choose projects carefully, sponsor them effectively and pursue them aggressively to completion. Smaller institutions can often complete Lean projects in less time than larger ones. Make decisions slowly and collaboratively but implement them rapidly. Apply the adage think big, start small, show impact.
- See further by standing on the shoulders of giants. Higher education institutions are undoubtedly collaborative and can provide a valuable support network to those embarking and continuing on their Lean journey. In particular, the Lean HE group, www.leanhe.org, provides exemplary peer support and promotion of Lean HE best practice.
4. Innovate your “own best way”. There is no “one best way”. Therefore, develop an organic, flexible approach to lean implementation that works for you. For example, rapid improvement events are not always the best solution for institutions with relatively lower headcount and subject matter experts with extensive operational commitments.
Find out more on the RCSI website and by following us on our official Twitter @rcsi_irl, Instagram @RCSI_Irl, Facebook, LinkedIn and YouTube channels.